Adaptive Strategies: New Worksite Safety and the Impact on Owner Costs
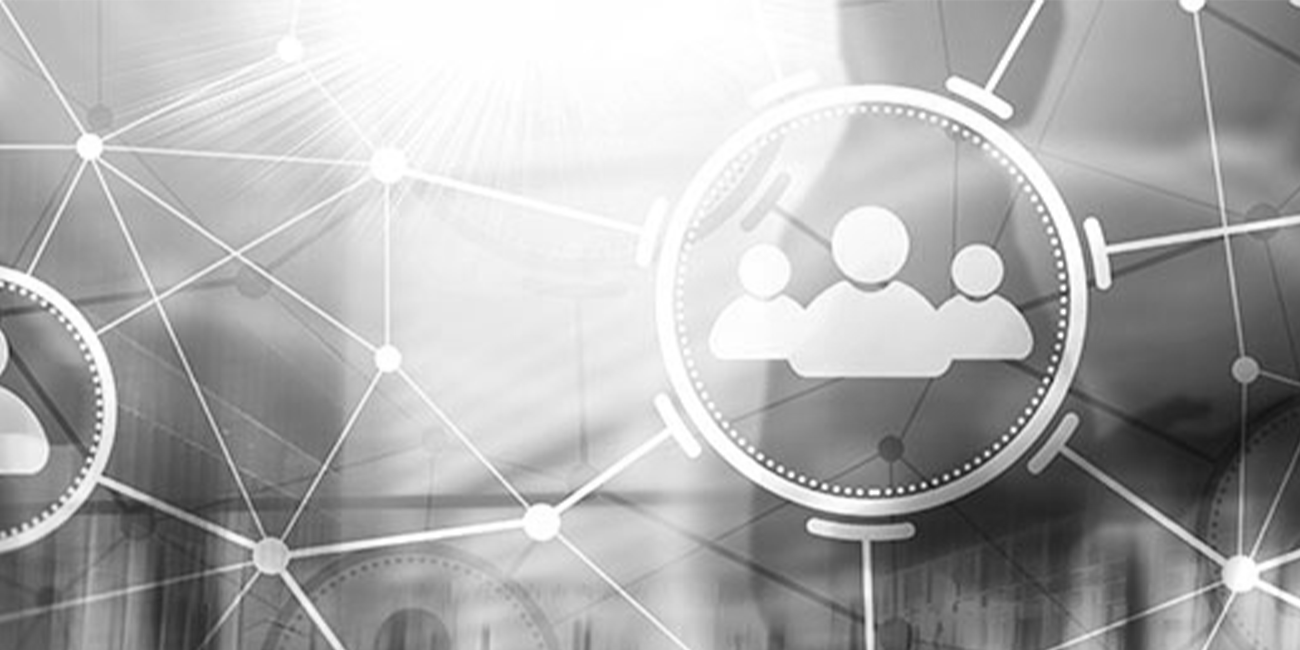
Adaptive Strategies: New Worksite Safety and the Impact on Owner Costs
While safety has always been a top priority on project job sites, COVID-19 is dramatically expanding the parameters of worksite protections. General contractors (GC’s) across the country are evolving their safety protocols to safeguard the welfare of workers and, in some regions, appropriately respond to state and/or local mandates.
Each of these interventions comes with a cost and, in most cases, owners are likely going to be responsible for the additional expenses.
PMA continues sharing adaptive strategies from across the country in an effort to offer insight to project challenges you may be facing now or in the future.
Are there adaptive strategies you’d like to share? We’re all ears. We’re all #inthistogether.
How do GC’s know who is on the job site?
Most projects have implemented some kind of formalized process to check-in workers each day as they arrive on a site. Prior to entry, they are asked a series of questions so that GC’s are able to track who is working on what and with whom.
Funneling each worker through this process creates a pinch point that delays work commencement and decreases production. Furthermore, having a staff member manage this process increases expenses.
On some job sites, Quick Response (QR) code technology is being utilized to expedite this daily check-in process and reduce costs. Each worker uses their phone to scan a QR code mounted at the designated entrance gate. The QR code connects to a website or app containing a questionnaire that the worker then completes. By submitting their own data each morning, workers are self-administering their own check-in, expediting the check-in and eliminating the need for compliance staff.
Confidentially managed by the GC, this data is intended to help provide a swift and decisive response if a job site worker tests positive for the COVID-19 virus. The following is an outline of general steps being taken on a job site when such a case is identified:
• All work paused
• As a form of tracing, assess worker check-in data to determine whether others were exposed
• Project-wide notification of the incident
• Diagnosed individual quarantined (if not hospitalized)
• Exposed individuals potentially quarantined
• Project site is thoroughly sanitized / disinfected pursuant to CDC guidelines
• Project re-opens
Moving forward, how will GC’s plan for work in an occupied building?
As some areas of the country begin to open up and people consider returning to their offices, GC’s are beginning to contemplate how to safely and efficiently manage tenant improvement projects inside an occupied building.
Beyond the limitations of job-entry protocols outlined above, project logistics that hinge on access to freight elevator(s) are a significant and common concern. Distancing mandates in many states restrict the number of individuals that can be in an elevator at a given time, slowing the movement of workers to and from the areas of the building in which they work. GC’s also use freight elevators for material delivery and trash removal throughout the day. On top of project-specific needs, the building landlord, tenants and general delivery services also require access to the freight elevator(s) in the case of an occupied building.
Comprehensive logistics planning involving all impacted parties will be critical to maximize efficiency of the freight elevator(s). Potential adaptive strategies include staggered start times for job workers and building occupants, utilizing second and third shifts for material delivery and waste removal as well as temporarily commandeering passenger elevators for general freight and/or project-related needs.
Job costs related to the pandemic are increasing for a myriad of reasons ranging from additional personnel hired to manage compliance to the implementation of multiple shifts, and from acquiring a QR system to providing hand-washing stations at a job site. All of these added costs are being pushed to the project owner, altering the risk management landscape. Two proactive strategies that are emerging include establishing specific contingency allowances for 1) COVID-related expenses and/or 2) acceleration which is designed to make up for time lost to COVID-related delays.
Multifamily Hotelization: Busting Myths, Supporting Realities
Several myths surround the idea of hotelization in the multifamily sector. In response, ApartmentBuildings.com reached out to apartment experts to explore—and bust—many of those incorrect assumptions.